Continuously improving the dimensional accuracy of investment castings and reducing waste products caused by oversize has always been one of the main goals pursued by investment casting workers at home and abroad.
1. Dimensional stability of investment castings
1. Dimensional stability of wax model and its influencing factors
In most cases, the size of the wax mold fluctuates greatly when the size of the casting fluctuates, and there are a few exceptions. Overall, the size fluctuation of the wax mold accounts for 10% to 70% of the size fluctuation of the casting.
The molding process parameters have a decisive influence on the dimensional stability of the wax mold. The main factors are as follows:
(1) Wax pressing temperature
Different molding materials have different performances due to the influence of wax pressing temperature. When wax-based molding materials are used, the wax pressing temperature is very sensitive to the influence of wax mold dimensional stability, while resin-based molding materials have less influence.
(2) Injection pressure
When the pressure is small, the shrinkage rate of the wax mold decreases significantly when the pressure increases. However, after the pressure is increased to a certain extent (≥1.6MPa), the pressure has almost no effect on the size of the wax mold. It is no wonder that foreign test results often conclude that “the pressure has nothing to do with the size of the wax mold”, but the impression of many domestic companies is not entirely the same.
(3) Flow rate
The flow rate of the mold material can be changed in the following two ways, but the influence on the size of the wax mold is not the same:
·By changing the flow speed setting of the wax press, this method has little effect on the shrinkage of the wax mold. However, it has an important influence on the filling and surface quality of thin-walled parts with complex shapes or wax molds with cores.
·This method has a great influence by changing the cross-sectional area of the wax injection port, because increasing the cross-sectional area of the wax injection port can not only reduce the wax pressing temperature, but also prolong the solidification time of the mold material at the wax injection port, thereby increasing the wax mold compaction The degree of shrinkage and surface shrinkage are reduced.
(4) Injection time
The so-called injection time here includes three time periods of filling, compacting and maintaining. Filling time refers to the time for the molding material to fill the molding cavity; compaction refers to the time from filling the molding to the closing of the wax injection nozzle; and holding refers to the time from the wax injection nozzle closing to the ejection of the mold.
The injection time has a significant effect on the shrinkage rate of the wax mold. This is because more mold material may be squeezed into the cavity by increasing the injection time, and the wax mold will be more compacted, thereby reducing the shrinkage rate. The weight of the wax model increases with the prolonged compaction time. The compaction time should be appropriate. If the compaction time is too long, the mold material at the wax injection port has completely solidified, and the compaction will not work. It can also be seen from Figure 4 that when the injection time is short (15-25s), the wax pressing temperature rises, and the shrinkage rate increases; but when the injection time is extended to 25-35s (under the premise that the filling time remains constant, the actual The above is to extend the compaction time) The influence of the wax pressing temperature becomes smaller; when the injection time increases to more than 35s, the opposite situation will occur, that is, as the wax pressing temperature rises, the wax mold shrinkage rate will decrease instead. This phenomenon can be explained as that increasing the mold material temperature and prolonging the compaction time have the same effect as increasing the degree of wax mold compaction.
(5) Molding temperature and wax pressing equipment
The molding temperature is high, the wax mold cools slowly, and the shrinkage rate increases. This is because the wax mold is still in the compression molding before the mold is ejected, and the shrinkage is limited, but after the mold is ejected, it becomes free to shrink. Therefore, if the wax mold temperature is high when the mold is released, the final shrinkage rate will be large, and vice versa, the shrinkage rate will be small.
In the same way, the cooling system of the wax press may have an impact of about 0.3% on the size of the wax mold.
Finally, it is worth emphasizing that when using wax-based mold materials, wax paste is a three-phase coexistence system of solid, liquid and gas. The volume ratio between the three phases has a great influence on the size of the wax mold. The proportional relationship between these three cannot be controlled in actual production, which is also an important reason for the poor dimensional stability of wax molds using wax-based molding materials.
2. The influence of shell material and shell making process on the dimensional stability of castings
The influence of the mold shell on the size of the casting is mainly caused by the thermal expansion and thermal deformation (high temperature creep) of the mold shell during firing, and the restriction (obstruction) of the mold shell on the cooling shrinkage of the casting.
(1) Thermal expansion of shell
Mainly depends on the shell material. Different refractory materials have different expansion rates. Among the commonly used refractories, fused silica has the smallest expansion rate, followed by aluminum silicate, and silica is the largest and uneven. After testing, it is determined that the aluminum silicate shell can be heated from room temperature to 1000 ℃, the shell can produce about 0.25% expansion, which accounts for a small proportion of the overall shrinkage of the casting size. Therefore, if such refractory materials are used, the shell It has better dimensional stability, such as fused silica will undoubtedly be better. However, if silica is used, the size of the shell fluctuates greatly.
(2) Thermal deformation (high temperature creep)
For example, a shell using water glass as a binder has a significantly greater creep degree at high temperatures above 1000°C than that of silica sol and ethyl silicate shells. Although the fused corundum itself has high refractoriness, because of the presence of impurities such as sodium oxide, the shell firing temperature higher than 1000 ℃ may also cause creep, resulting in poor dimensional stability.
(3) The restraint of the mold shell on the shrinkage of the casting—the retreat and collapsibility of the mold shell This also mainly depends on the material of the mold shell.
In summary, refractory materials play a major role in the influence of the shell on the size fluctuation of the casting, but the role of the binder cannot be ignored. In contrast, the impact of the shell-making process is small.
3. The influence of stress caused by uneven cooling of castings on dimensional stability
The cooling rate of each part of the casting (including the gating system) is different, which generates thermal stress and deforms the casting, thereby affecting the dimensional stability. This is often encountered in actual production. Reducing the cooling rate of castings and improving the combination of runners are effective preventive measures.
2. The key to improving accuracy-mold shrinkage rate is assigned correctly
The above-mentioned “dimensional stability” is different from “dimensional accuracy” and “precision (precision)”. Dimensional stability (ie precision) is synonymous with dimensional consistency, reflecting the degree of dimensional fluctuation or dispersion, and is usually measured by the standard deviation σ. The main cause of dimensional instability is lax process control, which is a random error. Accuracy refers to the degree to which the arithmetic mean of many measured values deviates from the nominal size for a certain size on the casting, that is, the size of the average deviation. For investment casting, the main reason for the poor dimensional accuracy is the improper assignment of the shrinkage rate during the profiling design, which is a systematic error, which is usually adjusted by repeatedly repairing the mold. The dimensional accuracy (precision) is a combination of the above two. Therefore, to improve the dimensional accuracy of castings and solve the problem of product size tolerances, not only must the process be strictly controlled to reduce dimensional fluctuations, but also the shrinkage rate of each dimension of the casting must be correctly assigned when designing the profile.
It is well known that the final total shrinkage of precision castings is a combination of wax mold, alloy shrinkage and a small amount of shell expansion. The shell swells by about 0.25%, and its effect is limited. Although the linear shrinkage rate of the alloy is often greater than that of the wax mold, the dimensional fluctuation caused by the wax pressing process has a greater impact. In order to reduce the cost of mold repair and reduce the fluctuation of casting size, it is very important to control the shrinkage rate of the wax mold.
1. Wax mold shrinkage
The shrinkage of the wax mold should be measured after the size of the wax mold is completely stabilized. This is because the shrinkage of the wax mold does not stop completely after the mold is ejected. The size of the wax mold sometimes stabilizes only a few days after the mold is ejected. However, most of the shrinkage of the mold material is basically completed within one to several hours after the mold is ejected. The wax mold shrinkage rate mainly has the following influencing factors:
(1) Type of mold material;
(2) Sectional size of wax model;
It is worth emphasizing that the cross-sectional size of the wax mold has a significant effect on the shrinkage rate. For example, the shrinkage rate of a typical unfilled mold material when pressing wax molds of different thicknesses. The thickness of the section of the wax mold should generally not exceed 13mm. When the thickness is greater than 13mm, the wall thickness can be reduced by using cold wax blocks or metal cores to achieve the purpose of reducing shrinkage, which is particularly important for non-filler mold materials.
Note: 1. The shrinkage rate of the water-soluble mold material is about 0.25%;
2. When using soluble cores, ceramic cores, or quartz glass tubes, there is no linear shrinkage of the wax mold in contact with the core;
(3) Core types
The cavity size of the wax mold is undoubtedly consistent with the shape of the core. Therefore, the use of cores has become a way to improve the dimensional accuracy of the cavity of the wax mold.
2. Alloy shrinkage
Alloy shrinkage mainly depends on the following factors:
· Cast alloy type and chemical composition;
· Casting geometry (including constraint state and section size);
· Casting parameters, such as pouring temperature, shell temperature, casting cooling rate, etc.;
· Use of ceramic cores, quartz glass tubes, etc.
Since the pouring temperature, shell temperature, casting cooling rate and other process parameters are generally strictly controlled by standard process cards during the production process, the size fluctuations caused by this are not large between different production batches. Even if the pouring temperature exceeds the range required by the process specification, the fluctuation of the casting size is usually not large. Similar to the wax mold, the section size of the casting and the constraints of the mold shell are the main factors that affect the shrinkage of the alloy. Experience shows that the shrinkage rate of the fully constrained size is 85% to 89% of the free shrinkage rate; the semi-constrained size is 94% to 95%.
3. The minimum number of the first batch of samples for measurement
The shrinkage rate listed above is empirical data based on past experience, not the real shrinkage rate. Design and manufacture molds according to these data, repair is inevitable. In order to improve the accuracy and success rate of repairs, and reduce the number of repairs, a key link is to carefully check the size of a sufficient number of trial casting samples. Because the size of the castings we produce cannot be exactly the same, so only when the number of measured samples is large enough, the average value obtained can be close to the true arithmetic average. From this, it is not difficult to see that the minimum number of measurement samples is directly related to the process capability of the production process to control product size consistency (Process Capability). If the castings are completely the same in size, then only one sample is required to be tested; Conversely, if the casting size fluctuates greatly,
It is necessary to measure a lot of samples to get more accurate shrinkage data. As mentioned earlier, the ability of the production process to control the size can be represented by the 6σ of the casting size produced by this process. From the current technological level of most investment foundries, Hp is mostly above 0.5, so the first batch of measurement samples generally requires at least 11 samples.
three. Measurement system analysis
When analyzing and solving product size problems, we must pay attention to the accuracy and reliability of the measurement system used. In addition to the frequent calibration of measuring instruments and equipment themselves, it is also important to minimize measurement errors. If the measurement system (including the operator and the operation method) has a large error, not only the rejects may be judged as qualified products, but also many qualified products may be misjudged as rejects, both of which may cause major accidents or unnecessary economic losses. The easiest way to determine whether a measurement system is suitable for a specific measurement task is to perform reproducibility and repeatability qualification tests. The so-called repeatability means that the same inspector uses the same instrument (or equipment) and method to inspect the same part and obtain the consistency of the results. Reproducibility refers to the consistency of results obtained by different operators using different instruments to check the same part. The American Automotive Industry Action Group (Automotive Industry Action Group) stipulates that the percentage of the integrated standard deviation of repeatability and reproducibility R&R in the standard deviation of the measured casting size fluctuations is ≤30% as the standard for the measurement system to meet the requirements [5]. In the measurement of some large-sized and complex-shaped castings, not all measurement systems can meet this requirement. The allowable measurement error when measuring molds should be smaller, usually 1/3.
four. Mold structure and processing level
It is well known that the mold structure and processing quality have an important influence on the size and geometry of the wax mold. For example, whether the positioning and clamping mechanism is accurate and reliable, whether the matching clearance of the movable parts (such as movable blocks, bolts, etc.) is appropriate, whether the drawing method is beneficial to ensure the dimensional accuracy of the castings, etc. Needless to say, for a considerable number of domestic investment casting plants, the level of mold design and manufacturing still needs to be improved urgently.
Fives. in conclusion
From the above analysis, it is not difficult to see that improving the dimensional accuracy of investment castings is a systematic project involving all aspects of the investment casting production process. The main points can be summarized as follows:
1) Strictly control the molding process parameters, especially the parameters that have a significant impact on the size of the casting.
2) Choose the appropriate shell material.
3) Collect, count and analyze data related to shrinkage in a correct method that conforms to statistical principles to improve the accuracy of shrinkage assignment.
4) Frequently monitor the measurement system (including equipment, inspection personnel and technology) to ensure that the repeatability and reproducibility errors meet the specified requirements.
5) Continuously improve the level of mold design and manufacturing.
6) Measures such as casting correction and stabilization heat treatment are still indispensable in many occasions
Please keep the source and address of this article for reprinting: Various factors affecting the dimensional stability of investment castings
Minghe Die Casting Company are dedicated to manufacture and provide quality and high performance Casting Parts(metal Die Casting parts range mainly include Thin-Wall Die Casting,Hot Chamber Die Casting,Cold Chamber Die Casting),Round Service(Die Casting Service,Cnc Machining,Mold Making,Surface Treatment).Any custom Aluminum die casting, magnesium or Zamak/zinc die casting and other castings requirements are welcome to contact us.
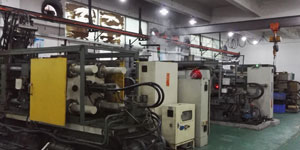
Under the control of ISO9001 and TS 16949,All processes are carried out through hundreds of advanced die casting machines, 5-axis machines, and other facilities, ranging from blasters to Ultra Sonic washing machines.Minghe not only has advanced equipment but also have professional team of experienced engineers,operators and inspectors to make the customer’s design come true.
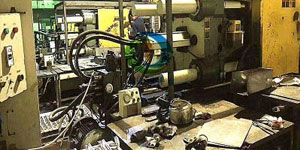
Contract manufacturer of die castings. Capabilities include cold chamber aluminum die casting parts from 0.15 lbs. to 6 lbs., quick change set up, and machining. Value-added services include polishing, vibrating, deburring, shot blasting, painting, plating, coating, assembly, and tooling. Materials worked with include alloys such as 360, 380, 383, and 413.
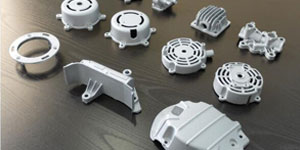
Zinc die casting design assistance/concurrent engineering services. Custom manufacturer of precision zinc die castings. Miniature castings, high pressure die castings, multi-slide mold castings, conventional mold castings, unit die and independent die castings and cavity sealed castings can be manufactured. Castings can be manufactured in lengths and widths up to 24 in. in +/-0.0005 in. tolerance.
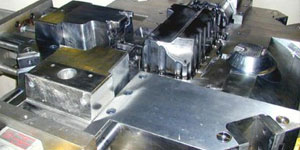
ISO 9001: 2015 certified manufacturer of die cast magnesium, Capabilities include high-pressure magnesium die casting up to 200 ton hot chamber & 3000 ton cold chamber, tooling design, polishing, molding, machining, powder & liquid painting, full QA with CMM capabilities, assembly, packaging & delivery.
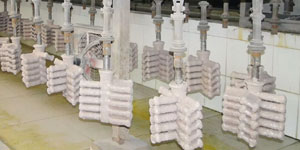
ITAF16949 certified. Additional Casting Service Include investment casting,sand casting,Gravity Casting, Lost Foam Casting,Centrifugal Casting,Vacuum Casting,Permanent Mold Casting,.Capabilities include EDI, engineering assistance, solid modeling and secondary processing.
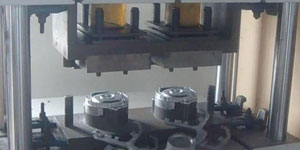
Casting Industries Parts Case Studies for: Cars, Bikes, Aircraft, Musical instruments, Watercraft, Optical devices, Sensors, Models, Electronic devices, Enclosures, Clocks, Machinery, Engines, Furniture, Jewelry, Jigs, Telecom, Lighting, Medical devices, Photographic devices, Robots, Sculptures, Sound equipment, Sporting equipment, Tooling, Toys and more.
What Can we help you do next?
∇ Go To Homepage For Die Casting China
→Casting Parts-Find out what we have done.
→Ralated Tips About Die Casting Services
By Minghe Die Casting Manufacturer |Categories: Helpful Articles |Material Tags: Aluminum Casting, Zinc Casting, Magnesium Casting, Titanium Casting, Stainless Steel Casting, Brass Casting,Bronze Casting,Casting Video,Company History,Aluminum Die Casting |Comments Off
Link to this article:Various factors affecting the dimensional stability of investment castings
Reprint Statement: If there are no special instructions, all articles on this site are original. Please indicate the source for reprinting:Tungusten,Thanks!^^