Oxidized pellets have good mechanical strength and metallurgical properties, and have become an indispensable high-quality charge for blast furnace ironmaking. However, the lack of domestic supply of magnetite concentrate has caused many domestic steel plants to use imported hematite to produce oxide pellets. Compared with magnetite pellets, hematite pellets have a high roasting temperature and a narrow range (1300℃~1350℃), and the pellets have low compressive strength. In addition, the acidic hematite pellets have poor metallurgical properties. Among them, specularite belongs to an important type of hematite, and the roasting performance and metallurgical properties of pellets are worse than ordinary hematite pellets.
Researchers have conducted a lot of research on how to use hematite to produce high-strength oxidized pellets. Studies have shown that adding magnetite to hematite to prepare oxidized pellets can effectively reduce the preheating roasting temperature and increase the compressive strength of the preheated roasting pellets; adding flux to produce fluxed hematite pellets is also a solution.
Domestic pellet plants generally use hematite and magnetite to produce high-strength pellets, but as the ratio of hematite increases, the effect of adding magnetite is greatly weakened. Adding CaO flux to produce flux pellets can obtain higher mechanical strength and better reducibility at a lower temperature, but the high-temperature reflow performance is poor and the reduction expansion is serious. Early studies have shown that adding MgO to the pellets can reduce the reduction expansion rate and improve the high-temperature reflow performance.
At present, there are relatively few reports on the effect of alkalinity and MgO content on the strength and metallurgical properties of specularite pellets, especially the effect of alkalinity and MgO on the metallurgical properties of pellets. Therefore, this article Studying the effects of alkalinity and MgO content on the strength and metallurgical properties of specularite pellets has important theoretical value for improving pellet roasting and strengthening blast furnace ironmaking.
Raw material properties and research methods
The raw materials used in this experiment are Brazilian specularite, bentonite, limestone and magnesite. Because Brazilian specularite, limestone, and magnesite are relatively coarse in particle size, they are ground to the particle size and specific surface area required for pellet production with a ball mill in the laboratory. Spiegelite has high iron grade, less gangue minerals and other harmful impurities, and is a high-quality pellet raw material. Limestone and magnesite have low SiO2 content and few other harmful impurities. They are high-quality calcium-magnesium fluxes.
The binder used in the test is high-quality sodium-based bentonite, and the indicators are as follows: the content of montmorillonite is 92.76%, the swelling volume is 20mL/g, the water absorption rate in 2 hours is 342%, and the content of -0.074mm reaches 100%.
The experimental research includes the process of batching, mixing, green ball preparation, green ball drying, dry ball preheating roasting and roasting pellet performance testing. The SiO2 content of the finished pellets is controlled at 3.0%~3.1% by adding finely ground quartz sand. The alkalinity and MgO content of the finished pellets are adjusted by adding limestone and magnesite, and the effects of changes in alkalinity and MgO content on the compressive strength, reduction degree, reduction expansion, low-temperature reduction pulverization and high-temperature soft-melting characteristics of the roasted pellets are investigated. Influence.
Test results and impact analysis
“The effect of alkalinity and MgO content on compressive strength and porosity.” The compressive strength of pellets is an important indicator reflecting the pressure that the pellets can withstand during the transportation and storage process and in the reduction furnace. Large blast furnaces require the compressive strength of pellets to be more than 2500 N/piece.
Under natural MgO content, the compressive strength of pellets first increases with the increase in alkalinity. When the alkalinity increases to 0.2, the compressive strength of pellets increases from 2400 N/piece of natural alkalinity to 3,500 N/piece; After reaching 0.4, the compressive strength of pellets no longer increases. This is due to the increase in alkalinity of CaO, Fe2O3 and SiO2, such as calcium ferrite and calcium silicate. The proper liquid phase is conducive to the recrystallization of hematite, but too much liquid phase is not conducive to the improvement of the compressive strength of the pellets. Under natural alkalinity, the compressive strength of the pellets decreases with the increase of MgO content. This is because the magnesite decomposes during the preheating and roasting of the pellets, which increases the porosity of the pellets.
When alkalinity and MgO work together, under the same MgO content, the effect of alkalinity on the compressive strength of the calcined pellets is basically the same as the effect of alkalinity on the compressive strength of the pellets under the natural MgO content, that is, the compressive strength of the pellets. The strength first increases with the increase of alkalinity. After the alkalinity reaches a certain value, the compressive strength of the pellets no longer increases significantly; under the same alkalinity, the compressive strength of the pellets decreases with the increase of MgO content, which is due to the MgO content As the increase, the porosity of the pellets increases, and at the same time MgO enters the slag phase to increase the melting point of the gangue minerals, which has a certain hindering effect on the formation of the liquid phase. The test results show that when the alkalinity is above 0.2, the compressive strength of specularite pellets with different alkalinity and MgO content can reach more than 2500 N/piece.
As the amount of flux increases, the pores left by the decomposition of the flux during preheating roasting also increase. The addition of flux not only affects the chemical composition and mineral composition of the pellets, but also affects the structure and porosity of the pellets. This will affect the compressive strength and metallurgical properties of the pellets to a certain extent.
The effect of alkalinity and MgO content on the degree of reduction. The degree of reduction (RI) is an important indicator for evaluating the tendency and difficulty of removing oxygen from iron ore under the conditions of temperature and atmosphere in the reduction zone of the blast furnace. The factors affecting the reduction degree of iron ore include particle size, porosity, mineral composition and structure, and gangue mineral composition.
The reduction degree of acidic pellets with natural alkalinity and natural MgO content is low, only 62.22%. With the increase of MgO content, the reduction degree increases. When the MgO content is 3.0%, the reduction degree of the pellets can reach 68%; When the content of MgO increases the alkalinity, the reduction degree of specularite pellets is greatly improved. When the alkalinity increases to 1.2, the reduction degree of the pellets rises to 72.82%. This is because the addition of limestone increases the porosity of the pellets, and at the same time, CaO reacts with Fe2O3 to form easily reduced calcium ferrite.
When alkalinity and MgO act together, under the same alkalinity, the degree of reduction of mirrorite pellets increases with the increase of MgO content; under the same MgO content, the degree of reduction increases with the increase of alkalinity.
When the alkalinity reaches 1.2 and the MgO content increases to 3.0%, the reduction degree of pellets is as high as 76.94%. This is because the magnesite also increases the porosity of the pellets during the preheating and roasting of the pellets, and MgO can increase the melting point of the slag phase and the floating body, so that it is not easy to melt during the reduction process, and the pores of the pellets are not melted. The material is filled to maintain a high porosity, which is conducive to gas diffusion.
The effect of alkalinity and MgO content on reduction expansion.
Under the natural MgO content, the reduction expansion rate of specularite pellets first increases and then decreases, and the alkalinity reaches the maximum value between 0.4 and 0.6, and the maximum value is as high as 32%.
This is because a small part of the CaO added to the pellets reacts with Fe2O3 to produce calcium ferrite, and most of it enters the slag phase. When it is not reduced, the slag phase is dominated by the CaO-SiO2 binary system. When the alkalinity is between 0.4 and 0.6, that is, the content of SiO2 in the slag phase is between 62.5% and 70%, which is the interval of the binary eutectic point composition of calcium metasilicate (CaOSiO2) and SiO2, and its low temperature eutectic point is 1436℃, but under reducing conditions, this slag phase becomes CaO-SiO2-FeO ternary slag system due to the addition of FeO. In this slag system, the ratio of CaO and SiO2 remains unchanged. The melting point of the slag phase increases sharply with the increase of FeO content. In the pure ternary slag system, it can be as low as 1093℃, and the low melting point slag phase will just worsen the reduction and expansion of the pellets.
Under natural alkalinity, the reduction expansion rate of pellets decreases slightly with the increase of MgO content, but it is not obvious. This is due to the natural alkalinity and natural MgO pellet slag phase with a melting point of 1700℃ when the content of SiO2 is 90%. With the addition of MgO, the slag phase is dominated by the MgO-SiO2 binary system, but its low-temperature eutectic temperature also has a low eutectic temperature. 1543°C. When the alkalinity and MgO work together, the effect of alkalinity on the reduction expansion rate of pellets is basically the same as the natural MgO content under the same MgO content. When MgO is added, the melting point of the slag phase is increased by the melting of MgO into the slag phase. At the same time, the melting point of the slag phase is also increased by MgO in the slag phase.
Therefore, under the same alkalinity, increasing the MgO content can reduce the reduction expansion.
The volume expansion of the hematite in the oxidized pellets is reduced to magnetite and floatite. This expansion is mainly caused by the change of the crystal structure when the hematite is reduced to magnetite. The reduction expansion rate of pellets is related to the gangue composition and the ability of the slag phase to withstand the stress generated by the reduction of hematite particles.
The high melting point slag phase is not easy to melt during the reduction process, and maintaining high strength can effectively limit the reduction expansion rate of the pellets, while the low melting point slag phase will worsen the reduction expansion of the pellets.
The reduction expansion rate of pellets below 20% belongs to the normal expansion range, and the alkalinity of specularite pellets should be controlled within the range of less than 0.2 or greater than or equal to 1.0.
However, in general industrial production, the reduction expansion rate of pellets is required to be controlled below 15%. For specularite pellets with natural alkalinity containing 3.0%~3.1% SiO2, the reduction expansion rate is less than 15%, and the reduction degree is only 62.2%. When improving the reduction degree by increasing the alkalinity, it is necessary to reduce the alkalinity Only when the degree of increase to 1.0 and the MgO content to 3.0%, or the alkalinity to 1.2 and the MgO content ≥1.0%, can the reduction expansion rate be lower than 15%.
The effect of alkalinity and MgO content on low-temperature reduction pulverization. Low temperature reduction pulverization (RDI) reflects the tendency of pellets to produce powder when they are reduced in the upper part of the blast furnace or direct reduction shaft furnace at a temperature range of 400°C to 600°C. The main reason for low-temperature reduction and pulverization is the volume expansion and lattice distortion caused by the conversion of crystal structure when hematite is reduced to magnetite.
There are three main bonding methods formed when pellets are preheated and roasted:
Iron oxide recrystallization, silicate bonding and ferrite bonding.
Among them, hematite recrystallization bonding is the most common and strongest, but hematite is extremely unstable under reducing conditions, while the silicate bonding phase can be maintained when hematite is reduced to magnetite. Change.
Therefore, it is possible to increase this uniform distribution and maintain a stable bonding phase under low-temperature reduction conditions by adding a flux, so as to reduce the low-temperature reduction and pulverization of mirrorite pellets.
The pellets with natural alkalinity and natural MgO content are mainly hematite solid-phase diffusion consolidation, with less silicate binding phase. Therefore, more powder is produced during low-temperature reduction, and its RDI-3.15mm value is as high as 12.75. %. Under the natural MgO content, the alkalinity increased to 0.2, and the pellet low-temperature reduction pulverization rate RDI-3.15mm value quickly decreased to 0.52%; the alkalinity continued to increase, and the RDI-3.15mm value was basically maintained at about 0.5%. This is because the addition of CaO enables the pellets to form more silicate liquid phases that are stable during low-temperature reduction during preheating and calcination, thereby achieving the purpose of reducing the low-temperature reduction and pulverization of pellets.
Under natural alkalinity, increasing the content of MgO, the low-temperature reduction and pulverization rate of pellets, RDI-3.15mm, all drop below 3.0%. When the alkalinity and MgO work together, the RDI-3.15mm value of pellets in low-temperature reduction pulverization is low. RDI-3.15mm decreases with the increase in alkalinity, and slightly increases with the increase in MgO content. This is due to MgO It can hinder the formation of liquid phase silicate.
The effect of alkalinity and MgO content on reflow characteristics. The melting characteristics of pellets can reflect the formation of pellets in the soft melting zone at the lower part of the blast furnace and their performance in the soft melting zone. The reflow characteristics of the charge have a greater impact on the operation of the blast furnace. The softening temperature of the pellets is low and the reflow interval is wide, and the air permeability of the reflow zone in the lower part of the blast furnace will become poor, which is not conducive to the convection of the reducing gas and the charge and seriously affects the reduction process.
The acid pellets with natural alkalinity and natural MgO content begin to soften at 1009°C, and the dropping temperature is 1272°C. With natural MgO content, the alkalinity increases to 1.2, the softening temperature of the pellets increases to 1034°C, the softening interval and the softening interval are narrowed, and the dripping temperature also increases to 1299°C. When the alkalinity is 1.2, increasing the MgO content can increase the softening start temperature and the dripping temperature. When the MgO content is 1.0%, the pellet softening temperature will rise to 1072℃, the dripping temperature will reach 1319℃, the MgO content will continue to increase, and the pellet softening temperature will not With further increase, the dripping temperature has increased.
The reflow characteristics of pellets are mainly affected by the low-melting liquid phases such as fusterite and slag produced during reduction. The poor high-temperature reflow characteristics of acid pellets are mainly due to the low melting point of FeO-rich olivine slag phase during the reduction process, and the addition of MgO can increase the melting point of the slag phase. The formation of a solid solution with a high melting point will also play a role in improving the high-temperature reflow characteristics of the pellets.
Please keep the source and address of this article for reprinting: “Alkali” and “Magnesium” to improve pellet performance
Minghe Die Casting Company are dedicated to manufacture and provide quality and high performance Casting Parts(metal Die Casting parts range mainly include Thin-Wall Die Casting,Hot Chamber Die Casting,Cold Chamber Die Casting),Round Service(Die Casting Service,Cnc Machining,Mold Making,Surface Treatment).Any custom Aluminum die casting, magnesium or Zamak/zinc die casting and other castings requirements are welcome to contact us.
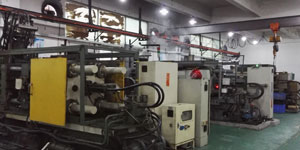
Under the control of ISO9001 and TS 16949,All processes are carried out through hundreds of advanced die casting machines, 5-axis machines, and other facilities, ranging from blasters to Ultra Sonic washing machines.Minghe not only has advanced equipment but also have professional team of experienced engineers,operators and inspectors to make the customer’s design come true.
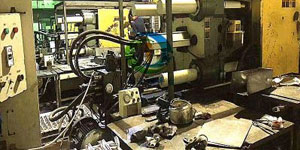
Contract manufacturer of die castings. Capabilities include cold chamber aluminum die casting parts from 0.15 lbs. to 6 lbs., quick change set up, and machining. Value-added services include polishing, vibrating, deburring, shot blasting, painting, plating, coating, assembly, and tooling. Materials worked with include alloys such as 360, 380, 383, and 413.
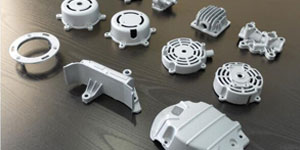
Zinc die casting design assistance/concurrent engineering services. Custom manufacturer of precision zinc die castings. Miniature castings, high pressure die castings, multi-slide mold castings, conventional mold castings, unit die and independent die castings and cavity sealed castings can be manufactured. Castings can be manufactured in lengths and widths up to 24 in. in +/-0.0005 in. tolerance.
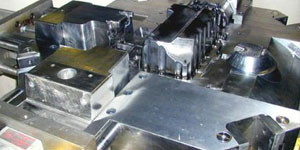
ISO 9001: 2015 certified manufacturer of die cast magnesium, Capabilities include high-pressure magnesium die casting up to 200 ton hot chamber & 3000 ton cold chamber, tooling design, polishing, molding, machining, powder & liquid painting, full QA with CMM capabilities, assembly, packaging & delivery.
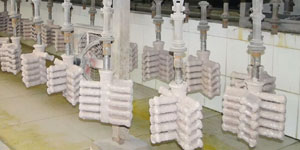
ITAF16949 certified. Additional Casting Service Include investment casting,sand casting,Gravity Casting, Lost Foam Casting,Centrifugal Casting,Vacuum Casting,Permanent Mold Casting,.Capabilities include EDI, engineering assistance, solid modeling and secondary processing.
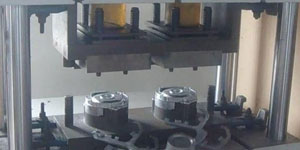
Casting Industries Parts Case Studies for: Cars, Bikes, Aircraft, Musical instruments, Watercraft, Optical devices, Sensors, Models, Electronic devices, Enclosures, Clocks, Machinery, Engines, Furniture, Jewelry, Jigs, Telecom, Lighting, Medical devices, Photographic devices, Robots, Sculptures, Sound equipment, Sporting equipment, Tooling, Toys and more.
What Can we help you do next?
∇ Go To Homepage For Die Casting China
→Casting Parts-Find out what we have done.
→Ralated Tips About Die Casting Services
By Minghe Die Casting Manufacturer |Categories: Helpful Articles |Material Tags: Aluminum Casting, Zinc Casting, Magnesium Casting, Titanium Casting, Stainless Steel Casting, Brass Casting,Bronze Casting,Casting Video,Company History,Aluminum Die Casting |Comments Off
Link to this article:"Alkali" and "Magnesium" to improve pellet performance
Reprint Statement: If there are no special instructions, all articles on this site are original. Please indicate the source for reprinting:Tungusten,Thanks!^^