3D printing is a rapid prototyping technology, based on digital model files, using powdered metal or plastic and other bondable materials to construct objects by layer-by-layer printing. Due to the characteristics of 3D printing such as fast speed, low cost, unlimited materials used for making prototypes, the ability to process parts of various shapes, flexibility and high degree of integration, titanium alloy 3D printing technology has developed rapidly in the aerospace field in recent years.
Due to the anisotropic characteristics of 3D printing titanium alloys, this paper analyzes the milling performance of 3D printed titanium alloys in different directions. At the same time, the cutting force, tool wear and other data were measured during the test, and the processing parameters were optimized according to the measured values. The difference in the cutting performance of two titanium alloy materials was compared to provide guidance for future processing and production.
1. Experimental conditions and scheme
(1) Test material
As shown in Figure 1, the test specimens are 3D printed titanium alloy blocks and forged TC4 titanium alloy blocks(can be used for TC4 Medical Ultrasound Bead Needle ), both of which are 40mm×30mm×20mm in size. Table 1 is the chemical composition of TC4 titanium alloy material.
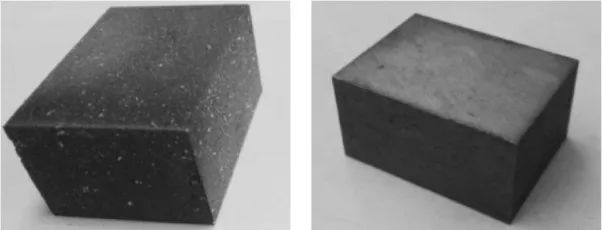
(a) 3D printed titanium alloy (b) forged TC4 titanium alloy
Figure 1 Test piece
Table 1 Chemical composition of TC4 titanium alloy materials (wt.%)
(2) Test equipment
- ① Processing machine tool: VMC850E processing center produced by Shenyang Machine Tool Factory;
- ②Processing tool: PVD diamond-coated carbide end mill, the tool parameters are D8*25*70*4T, the peripheral edge rake angle is 12°, the relief angle is 10°, and the helix angle is 40°;
- ③Measuring system: KISTLER9272 four-way piezoelectric force measuring instrument, KISTLER5017B charge amplifier and corresponding data acquisition and processing system;
- ④Others: Mitutoyo’s SJ201 surface roughness meter and A615 infrared thermal imager.
(3) Orthogonal test plan
The basic milling tests of 3D printed titanium alloy materials and TC4 titanium alloy materials were carried out respectively. The processing parameters are shown in Table 2, a total of 18 groups. There is no coolant during the test, which is convenient for temperature measurement during processing; up-cut milling is adopted.
Table 2 Milling parameters
2 Test results and analysis
(1) Analysis of milling force results
The line graph analysis of the milling force Fx of the two materials is shown in Figure 2.
Under the same milling parameters, the milling force Fx of the forged TC4 titanium alloy is greater than that of the 3D printed titanium alloy, and the milling force Fx of the former is not as obvious as that of the latter during high-speed milling. This is because although the strength (hardness) of the forged TC4 titanium alloy is slightly poor, its plasticity is very good, so during the processing, there will be large plastic deformation, easy to stick to the knife, etc., which will aggravate the wear of the tool and increase the titanium milling resistance, resulting in milling force larger. Although the 3D printing titanium alloy has high strength, it has low plasticity, and adiabatic temperature rise will occur at a large strain rate (see Figure 3), resulting in obvious softening of the material temperature rise and a sharp drop in milling force.
Comparing and analyzing the chips of the two materials (see Figure 4), it is found that the 3D printed titanium alloy chips have a smaller curl and a C-shaped sheet, which is easy to break chips and is not easy to wrap around the knife, and the plastic deformation is small when breaking chips, which generates heat. Less; TC4 titanium alloy chips have a large curling range and are cylindrical in shape, which is easy to entangle the chips and stick to the knife. When the chips are broken, the plastic deformation is large, more heat is generated, and the deformation resistance is also large. In summary, the forged TC4 titanium alloy has better plasticity and greater milling force during processing.
The range analysis of the milling force Fx is shown in Figure 5. It can be found that the linear speed has the greatest influence on the milling force of 3D printed titanium alloy, followed by the axial depth of cut, and finally the feed per tooth. When the line speed increases from 40m/min to 80m/min in turn, the milling force Fx first increases and then decreases. The increase of the feed per tooth and the axial depth of cut will lead to the increase of the milling force Fx, and the increment of the milling force caused by the increment of the axial depth of cut is obviously greater than the milling force caused by the increment of the feed per tooth Increment; for forged TC4 titanium alloy, the linear speed has the greatest influence on its milling force Fx, followed by the feed per tooth, and finally the axial depth of cut.
(2) Milling temperature analysis
It can be seen from Figure 6 that for 3D printed titanium alloys, since the plasticity is not as good as that of forged TC4 titanium alloys, the titanium cnc machining temperature of the former is lower than that of the latter under the same processing parameters. At a small linear speed, the milling temperature will decrease to a certain extent with the increase of the axial depth of cut, which is consistent with the forging TC4 titanium alloy. As the line speed gradually increases, especially when the line speed increases to 60m/min, the temperature suddenly rises from 470°C to 580°C because the line speed is high and the axial depth of cut is small, the extrusion effect between the tool and the workpiece surface It is more obvious, and the chips are smaller, so it will cause a certain temperature rise. With the further increase of the line speed to 80m/min, the change of milling temperature is no longer obvious, but presents a small amplitude oscillation. This is because the plasticity of 3D printed titanium alloy is poor, and a higher spindle speed can greatly reduce the plastic deformation of the material. Even if the spindle speed is increased, the plastic deformation is no longer obvious.
(3) Tool wear detection and analysis
It can be seen from Fig. 7a that the forged TC4 titanium alloy processing tool wears seriously, the chipping phenomenon at the peripheral edge is very obvious, the matrix material falls off seriously, and a large amount of titanium alloy matrix material is bonded to the tool peripheral edge. This is because during milling of titanium alloys, the high temperature in the cutting zone and the high chip strain rate will cause a certain degree of material softening, which will bond to the tool. With the increase of chip accumulation, the roughness of the tool edge increases and is no longer sharp, which further increases the cutting resistance. In addition, there are some cracks on the flank of the peripheral blade. As the cracks further increase, the cutting edge material will slowly fall off, exposing the tool base material. The peeling phenomenon of the coating on the flank is also relatively obvious, which makes the tool base material directly contact with the workpiece material, accelerates the abrasive wear and diffusion wear of the flank flank of the tool, and reduces the service life of the tool. It can be seen from Figure 7b that the rake face of the peripheral edge of the milling cutter wears lightly, basically only chipping and chip sticking occur near the cutting edge, and the phenomenon of abrasive wear is not obvious, which is more in line with the characteristics of up-cut milling.
The 3D printed titanium alloy processing tool also has micro chipping and matrix material shedding at the peripheral edge, and there are obvious abrasive wear scratches on the flank, but the bonding phenomenon of titanium alloy matrix material is not obvious on the peripheral flank (See Figure 8). This is due to the high hardness of the 3D printed titanium alloy material during the titanium alloy milling process, so the abrasive wear phenomenon is more serious during the processing process, resulting in very obvious abrasive wear scratches on the flank. Moreover, due to the high hardness and brittleness of the material, the base material will fall off after a small plastic deformation occurs during the processing, so the heat generated during the material removal process is less, and it is not easy to stick chips. The wear on the flank of the peripheral edge is basically the same as that of the forged TC4 titanium alloy.
Compared with the forged TC4 titanium alloy processing tool, the 3D printing titanium alloy processing tool has less wear, less micro chipping at the edge of the peripheral edge, and less obvious chip sticking on the flank of the peripheral edge. Therefore, under the same processing parameters, the 3D printing titanium alloy material processing tool has a longer life.
epilogue
- (1) Under the same milling parameters, the milling force Fx of the forged TC4 titanium alloy is greater than the milling force Fx of the 3D printed titanium alloy, and the milling force of the former is not as obvious as that of the latter during high-speed milling;
- (2) Under the same processing parameters, the milling temperature of 3D printed titanium alloy materials is lower than that of titanium alloy forgings;
- (3) Under the same processing parameters, the 3D printing titanium alloy material processing tool has a longer life;
- (4) When processing these two titanium alloy materials, the cutting speed should be avoided at around 60m/min. If conditions permit, low spindle speed and high feed speed can be used.
Link to this article:3D Printing Titanium vs CNC Machining Titanium
Reprint Statement: If there are no special instructions, all articles on this site are original. Please indicate the source for reprinting:Tungusten,Thanks!^^