The American Society of Metals Steel Casting Evaluation Committee divides steel castings into four major groups based on their carbon content. (a) Low carbon steel castings with a carbon content of less than 0.2%, (b) medium carbon steel castings with a carbon content of 0.2-0.5%, (c) high carbon steel castings with a carbon content of more than 0.5%, and (d) low alloy steel castings-limited to various grades of steel castings with a total alloy content of less than 8%. At present, China’s steel castings have surpassed the United States to become the world’s largest. Although the production is large, the added value of castings is relatively low. Developed countries such as the United States use high-tech to increase the added value of castings. American steel castings have two major performance characteristics: engineering performance and physical performance.
Engineering performance:
The wear resistance of cast steel is similar to that of forged steel with similar composition and morphology.
The corrosion resistance of cast steel is similar to that of forged steel with equivalent composition. The corrosion resistance data of forged carbon steel and low alloy steel in various states that have been published can be used for casting steel.
When the temperature is above 480-540 ℃, carbon steel and low alloy steel oxidize rapidly, and the formed oxide skin cannot protect the metal below the oxide skin from further oxidation. If these steels are exposed to such high temperatures for a long time, they will gradually become oxides. In order to effectively resist oxidation at high temperatures, high alloy steel must be used.
The welding performance of cast steel parts is similar to that of forged steel with the same composition, and the factors considered for welding cast steel parts are the same as those for forged steel parts.
Extensive turning and drilling tests on steel castings have shown that as long as the strength, hardness, and microstructure are comparable, there is no significant difference in machinability between steels produced by different melting processes, and there is no significant difference in machinability between forged steel and cast steel.
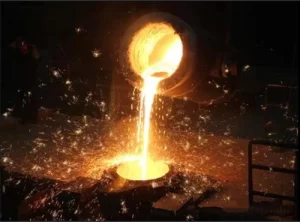
Physical performance:
The physical properties of cast steel are generally similar to those of forged steel.
The shrinkage from solidus to solid state at room temperature varies between 6.9-7.4. The alloying elements have no significant impact on this shrinkage. Metal that has just solidified has very low strength. The stiffness of the mold enables the shape of the casting to adapt well to this shrinkage condition, in order to successfully produce the casting. Due to shrinkage, many casting designs require extensive research to produce qualified castings.
The density of cast steel is highly sensitive to changes in composition, structure, and temperature. The density of cast steel is also somewhat influenced by the cross-sectional size or weight.
The changes in the composition and structure of the elastic modulus have only a small impact on the elastic constants of carbon steel and low alloy steel determined at room temperature. The increase in temperature has a significant impact on the elastic modulus and rigid modulus.
In developed countries, more and more casting industries are moving towards high-tech production, constantly improving the added value of casting products. China needs to move from a major casting country to a strong casting country, continuously strengthening basic and applied research in the casting industry, and overcoming the challenges of energy, resource, talent bottlenecks, and environmental problems in reality. Seize opportunities and improve the quality of castings.
This article is reprinted from website: https://steelcastingmfg.com/.
Link to this article:Performance characteristics of American steel castings
Reprint Statement: If there are no special instructions, all articles on this site are original. Please indicate the source for reprinting:Tungusten,Thanks!^^