Improving the cleanliness of the cast slab is the basis for the production of high-quality steel, and the total oxygen content of the cast slab is an important measure of the cleanliness of the molten steel. Reducing the total oxygen content of the cast slab is mainly carried out from three aspects: converter process, refining process and continuous casting process:
1, converter process
The converter process should implement high carbon pull rate and optimize the slag washing process.
(1) End pull carbon
Implement a less slag process, which strengthens the dephosphorization effect in the early stage, stabilizes the decarburization operation in the later stage, and then implements high-carbon control.
(2) Slag washing process
Promote the converter lime slag washing process, that is, during the converter tapping process, after the alloy is added, lime is directly added from the silo to the ladle along with the molten steel flow. This helps lime pre-melting in advance, promotes the slag to absorb inclusions for more time, and the initial slag can effectively cover the molten steel interface, reducing the probability of exposed molten steel to absorb oxygen.
2, refining process
The refining process should optimize the slag system, bottom argon blowing process, and calcium treatment process.
(1) Slag system optimization
The increase in the basicity of the slag is conducive to improving the deoxidizing capacity of the refining slag and reducing the oxygen content in the steel. At the same time, the slag should be reduced. This is because the SiO2 content in the slag is reduced, which greatly reduces the SiO2 activity coefficient, which can avoid or reduce the influence of the reaction between SiO2 in the slag and Al in the steel on the deoxidation of molten steel.
(2) Optimize the bottom blowing argon process
is mainly: (1) The entire refining process should use as little strong stirring as possible to reduce the exposure of molten steel and slag entrapment, and reduce the erosion of the ladle refractory material. (2) During the soft blowing process, pay attention to adjusting the argon gas so that the slag creeps, and the molten steel level is not exposed. (3) Before the VD reaches high vacuum, avoid excessive argon flow to expose molten steel; when reaching high vacuum, adjust the argon flow appropriately to ensure sufficient vacuum degassing effect and increase the reaction rate of slag steel.
(3) Calcium treatment process
Solid core pure calcium wire has obvious effect on Al2O3 inclusion denaturation. The calcium treatment process uses solid core pure calcium wire instead of silicon calcium and calcium iron cored wire.
3, continuous casting process
The continuous casting process mainly protects the pouring: argon replacement is used before pouring, and asbestos bowl gaskets are used for the large package casing to avoid secondary oxidation caused by oxygen absorption in the molten steel; the addition of the covering agent for the tundish must meet the requirements to ensure that the molten steel is not exposed and the slag layer No crusting; strengthen the monitoring and maintenance of the automatic monitoring system for slag under the ladle to ensure the normal operation of the system; ensure that the drainage sand is added to increase the self-opening rate of the pouring slide.
Please keep the source and address of this article for reprinting: Method of reducing total oxygen in slab
Minghe Die Casting Company are dedicated to manufacture and provide quality and high performance Casting Parts(metal Die Casting parts range mainly include Thin-Wall Die Casting,Hot Chamber Die Casting,Cold Chamber Die Casting),Round Service(Die Casting Service,Cnc Machining,Mold Making,Surface Treatment).Any custom Aluminum die casting, magnesium or Zamak/zinc die casting and other castings requirements are welcome to contact us.
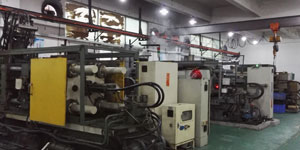
Under the control of ISO9001 and TS 16949,All processes are carried out through hundreds of advanced die casting machines, 5-axis machines, and other facilities, ranging from blasters to Ultra Sonic washing machines.Minghe not only has advanced equipment but also have professional team of experienced engineers,operators and inspectors to make the customer’s design come true.
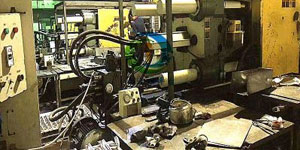
Contract manufacturer of die castings. Capabilities include cold chamber aluminum die casting parts from 0.15 lbs. to 6 lbs., quick change set up, and machining. Value-added services include polishing, vibrating, deburring, shot blasting, painting, plating, coating, assembly, and tooling. Materials worked with include alloys such as 360, 380, 383, and 413.

Zinc die casting design assistance/concurrent engineering services. Custom manufacturer of precision zinc die castings. Miniature castings, high pressure die castings, multi-slide mold castings, conventional mold castings, unit die and independent die castings and cavity sealed castings can be manufactured. Castings can be manufactured in lengths and widths up to 24 in. in +/-0.0005 in. tolerance.
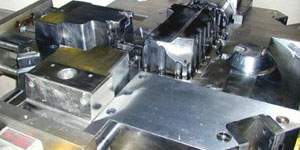
ISO 9001: 2015 certified manufacturer of die cast magnesium, Capabilities include high-pressure magnesium die casting up to 200 ton hot chamber & 3000 ton cold chamber, tooling design, polishing, molding, machining, powder & liquid painting, full QA with CMM capabilities, assembly, packaging & delivery.
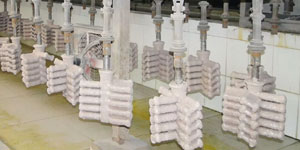
ITAF16949 certified. Additional Casting Service Include investment casting,sand casting,Gravity Casting, Lost Foam Casting,Centrifugal Casting,Vacuum Casting,Permanent Mold Casting,.Capabilities include EDI, engineering assistance, solid modeling and secondary processing.
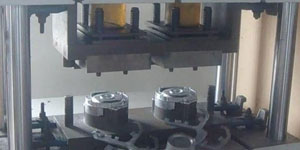
Casting Industries Parts Case Studies for: Cars, Bikes, Aircraft, Musical instruments, Watercraft, Optical devices, Sensors, Models, Electronic devices, Enclosures, Clocks, Machinery, Engines, Furniture, Jewelry, Jigs, Telecom, Lighting, Medical devices, Photographic devices, Robots, Sculptures, Sound equipment, Sporting equipment, Tooling, Toys and more.
What Can we help you do next?
∇ Go To Homepage For Die Casting China
→Casting Parts-Find out what we have done.
→Ralated Tips About Die Casting Services
By Minghe Die Casting Manufacturer |Categories: Helpful Articles |Material Tags: Aluminum Casting, Zinc Casting, Magnesium Casting, Titanium Casting, Stainless Steel Casting, Brass Casting,Bronze Casting,Casting Video,Company History,Aluminum Die Casting |Comments Off
Link to this article:Method of reducing total oxygen in slab
Reprint Statement: If there are no special instructions, all articles on this site are original. Please indicate the source for reprinting:Tungusten,Thanks!^^